With all industry projections pointing to a strong construction season ahead, we’ve spent the last 6 months making sure we can meet your requirements.
Multi-million-dollar investments in mobile equipment, plants and operations have helped Prairie gear up for better service in every region, says Jim Munro , President and General Manager, U.S Ready Mix, VCNA.
“We’re keenly aware of what our customers need and expect from us,” Munro says. “Falling short in 2015 isn’t an option.”
“For the first time in our company’s history, we kept all maintenance and mechanical staff on board all winter long to perform deep maintenance on our fleet and service yards,” says Prairie Maintenance Director Matt Clarage , describing the work we’ve done to assure readiness for the busy months ahead.
FLEET: New and upgraded trucks with 150 additional drivers
An ongoing fleet study revealed the need for greater capacity, so 35 new ready-mix trucks will hit the roads this year. Combined with 36 trucks added last year, Prairie’s system-wide fleet now numbers more than 650 mixers on the road.
In addition to new trucks, fleet maintenance crews have scoured each existing mixer for issues that could cause service disruptions. Many trucks received bumper-to-bumper overhauls, including new mixer drums.
Because safety is a constant priority, our fleet overhaul included installation of chute stops on all existing trucks.
“The chute requires drivers to use a free hand to hold out a wedge so that hands are kept out of harm’s way,” Clarage explains. “If contractors on the job site decide to help out, their hands are also protected when flipping the chute over.”
As mechanical upgrades go forward, Prairie People and Management Director Margaret Tyburski is leading the effort to hire 150 new delivery and bulk drivers to handle increased demand.
“We are offering top pay, generous benefits, and a 401k savings program along with 12 full days of classroom and behind-the-wheel training to ensure we get the best candidates,” she says.
SUPPLY: Plenty of cement on hand
Construction is moving forward on a new storage dome near Lake Calumet in Chicago to increase local Portland cement inventory. When the dome is completed later this year, it will provide an additional 55,000 metric tons of storage.
Our cement plant in Dixon, Illinois, will also reopen this season, providing additional Portland cement capacity to the Illinois market.
PLANTS: Major overhauls to prevent service interruptions
Yard maintenance teams, usually on standby during the winter months, instead worked through the cold season to tune up operations in all regions.
Crews performed bin repairs in Decatur, Morton and East Dundee, installed a new mixer liner at the dual-drum portable plant at Chicago’s O’Hare Airport and completed mixer liner replacements in Champaign.
Yard 32 in Chicago, where peak production reaches 4,000 yards per day, underwent a full overhaul to repair or replace critical plant equipment.
“In November, we shut down Plant 2 at Yard 32 to change out bin liners and bore out and replace pins and bushings,” says Clarage. “A crew of 6 workers spent 2 weeks in the plant re-lining the bins while a crew worked on repairing the turnhead that makes sure aggregates flow into the right bin.”
In December, Plant 1 was taken out of service to change out liners and blades, Clarage adds.
Large concrete silos that store all aggregate were emptied one by one for installation of new, stainless-steel heating pipes – a huge challenge, since Yard 32 ships thousands of yards per day, even in winter. New underground water lines feeding the heating system were also installed.
Heated aggregates, combined with heated water, enable us to maintain temperature standards, resulting in better quality control for concrete shipped during the coldest months of the year.
DISPATCH: Refreshing systems, workflows for reliable service
Prairie has added more dispatch and scheduling capacity to foster a closer relationship with all customers.
“We have upgraded our systems as part of our total effort to streamline workflow between central dispatch, plant management, customers and the field,” says Logistics Manager Brent Pommerening . “We’re also remodeling the office this May so that team members will work side by side. The goal is to give accurate, complete information to our customers, improving service as we build greater reliability.”
DEDICATED to your needs
“As the construction season kicks off, our goal is to be more than ready,” Jim Munro stresses. “We want to strengthen our customers’ trust by providing quality products, superior service, and doing what we say we will do.”
Here’s a look at current job openings.
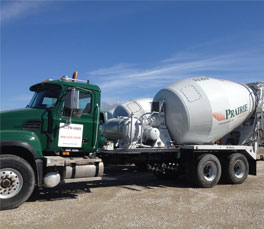